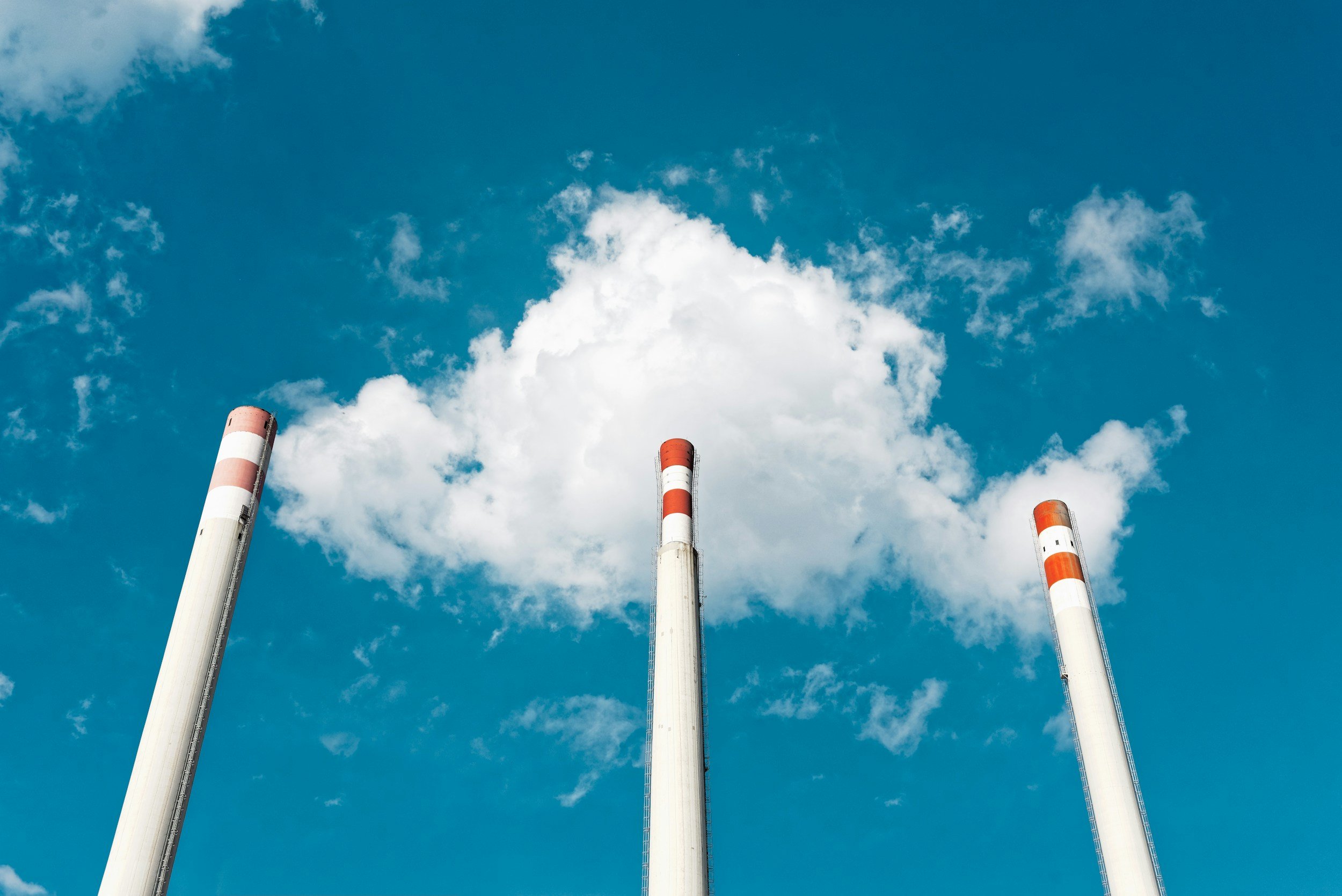
Inspection Service
Inspection Service
Boiler Inspection
Boiler remaining life assessment determines the safe operational lifespan by evaluating degradation from high pressure, temperature, and operational stress. Key factors include material properties, operational history, and maintenance practices. Various latest technologies available in Non-destructive and destructive tests will be used to assess the present status of each component. The purpose of RLA activity is not to continue the operation of a plant beyond its design life, but merely to ensure full utilization up to its useful life.
Key Factors Affecting Lifespan
Material Degradation : Creep, fatigue, thermal cycling, and embrittlement.
Corrosion/Erosion : Caused by poor water chemistry, scaling, or fuel type (coal,gas, oil).
Design Specifications : MAWP, temperature, and material types (e.g., carbon steel, alloys).
Operational History : Cycles (startups/shutdowns), overload incidents, and maintenance quality.
Non-Destructive Testing (NDT) method
Ultrasonic Testing (UT) : Thickness measurements of tubes/drums.
Penetrant (PT) & Magnetic Particle (MT) : Surface cracks.
Radiography (RT) : Internal weld flaws.
Hardness Testing : Detects embrittlement
Metallurgical Examination will assess microstructural degradation caused by high temperature, creep, corrosion, or other factors.
Replica Metallography : Non-invasive replication of surface microstructure.
Scanning Electron Microscopy (SEM) : Detailed analysis of grain structure, cracking, and surface conditions.
Hardness Testing : Assesses mechanical strength loss
Creep Life Assessment
Creep (time-dependent deformation under high temperature/stress) is a primary failure mechanism in boilers.
Larson-Miller Parameter (LMP):
Estimates creep life using temperature and stress data:
LMP = T * (log t + C)
Where (T) = temperature (Kelvin), (t) = time (hours), (C) = material constant.
Replica Testing (Metallurgical Replication)
is a non-destructive evaluation (NDE) method used to assess the microstructural condition* of boiler components exposed to high temperatures and stresses. It helps identify degradation mechanisms like creep damage, spheroidization, or graphitization without removing material samples. Here’s a detailed breakdown:
Purpose of Replica Testing
Detect Microstructural Changes: Identifies creep voids, carbide coarsening, or intergranular cracks caused by prolonged high-temperature operation. Monitor Material Degradation: Evaluates aging in critical components (e.g., superheater tubes, headers, steam drums). Support Remaining Life Assessment: Provides data to estimate residual creep life or fatigue resistance.
Case
